Automation blog
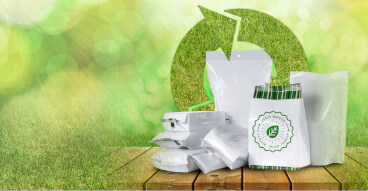
Green packaging industry: How to achieve sustainable manufacturing
09 February, 2022 Sustainability in the packaging industry is one of the key aspects in fighting the plastic waste issue and ultimately climate change. The challenges that this presents, require flexible and powerful automation technology.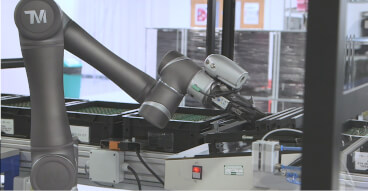
Hanover Displays automates PCBA testing with cobots
31 January, 2022 UK-based Hanover Displays Limited needed a new system for testing printed circuit board assemblies (PCBAs) and selected OMRON TM cobots for the job, supplied and installed by Absolute Robotics, part of the Absolute Automation Group.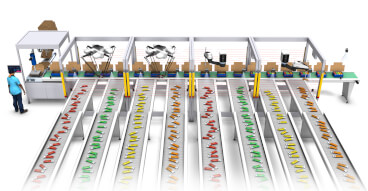
Five challenges in High-Mix, Low-Volume (HMLV) packaging and palletizing processes
21 December, 2021 The new product has just left the factory, in a shelf-ready package in the specified mixed ratio to meet customer needs. The packaging has actually been handled by another company: a co-packer. Co-packing can be found in all Fast-Moving Consumer Goods (FMCG) markets, but especially in the higher-priced product segments such as personal care or confectionery, to name a few examples. It is a fast-growing activity to satisfy the consumer demand for more variety.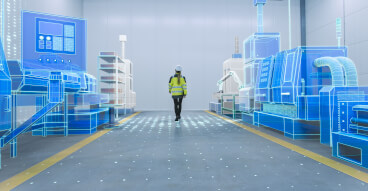
Productivity Peaks: Moving Maintenance From Preventive to Predictive
17 December, 2021 Maintenance is a vital key to a thriving business, especially in manufacturing where 24/7 plant equipment uptime is often expected as standard. As any established enterprise knows, keeping production lines and systems running optimally requires more than a skilled maintenance team. It also involves careful planning, tight scheduling, constant vigilance, a willingness to change out unworn parts, and a readiness to respond to unplanned events. At least, it used to.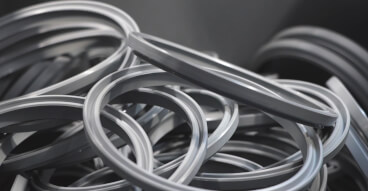
Finished seals in less than 10 seconds: Robotics Integrated Controller ensures harmonious control
24 November, 2021 Trelleborg Livorno has updated a robotic cell for the finishing of polyurethane gaskets for the sustainable wind energy market. The cornerstone of the solution is OMRON's Robotics Integrated Controller that ensures integration and synchronization of all automation components, including robots, logic, motion, safety and user interface.
FasThink optimizes Garnet's intralogistics with mobile robots
02 November, 2021 Garnet relies on FasThink to innovate its logistics and production processes.
Intelligent System Solutions with Autonomous Mobile Robot: AM-Flow and OMRON
27 October, 2021 Industry 4.0 brings the promise of streamlined processes, big data insights and production lines running 24/7 with zero downtime. Unlike historical ‘industrial revolutions,’ this one offers the luxury of time and choice for manufacturers. That’s because the benefits of automation can be embraced incrementally or fully, whether it’s a new state-of-the-art facility or something retrofit-installed into a more traditional production setup. Making it easier to make the move is AM-Flow, an entrepreneurial start-up currently making waves in providing its solutions to the new tide of producers coming ashore in the world of additive manufacturing.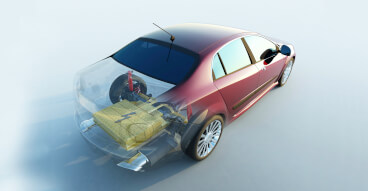
Fuelling the success of local battery cell production
20 September, 2021 Expert and automotive manufacturers alike agree that e-mobility is the future. Batteries and battery manufacturing are central to this development. In this context, the global market for lithium-ion batteries is expected to grow from 44.2 billion US dollars (2020) to 94.4 billion dollars (2025). The transformation of the automotive industry from internal combustion engines to battery or hydrogen-powered fuel cells is presenting companies with immense challenges.
Developing digital capability: how any factory can be smart
16 September, 2021 Thankfully, the headline-grabbing ‘Industry 4.0’ isn’t reserved exclusively for the high-tech giants that span the globe, nor is the term ‘smart factory’ applied only to brand-new installations. In truth, any traditional factory can in principle take steps on the smart factory journey, by applying modularity to the existing installation.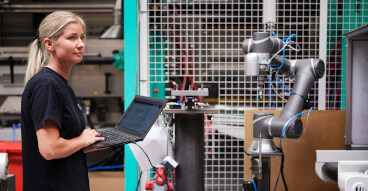
Unika makes Landmark decision to bring quality levels to new heights
25 August, 2021 OMRON TM cobots with integrated vision system eliminate human error, increase production efficiency.
Flexible, safe and easy collaborative welding solution from Guidetti Technology
20 August, 2021 Guidetti Technology SRL has integrated OMRON collaborative robots (cobots) into its ‘EasyArc’ welding solution. This is used in collaborative applications on small batches of various types of metal carpentry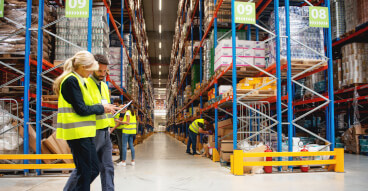
How labour shortages are affecting the logistics sector and why automation is the solution
11 August, 2021 By Stuart Coulton, Regional Manager, OMRON UK North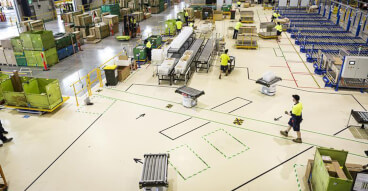
Mobile robots smarten up Toyota’s new parts centre
28 April, 2020 Intelligent robots and sophisticated design are helping Toyota to achieve a higher level of efficiency at its new warehouse in Sydney, Australia.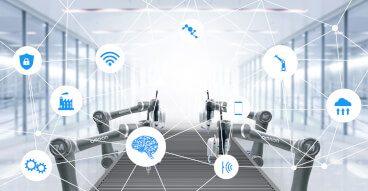
Cobot and flexible production - Future-proofing SMEs?
17 March, 2020 Many countries in Europe, such as the UK and Germany are likely to experience serious labour shortages over the coming decade, especially in relation to technical specialists. At the same time, product lifecycles are becoming shorter. Despite this, small and medium-sized enterprises (SMEs) might be reluctant to invest in additional automation. However, collaborative robots (cobots) are easy to set up and offer a quick and cost-effective solution. They can increase the flexibility, quality and speed of production and enable companies to respond rapidly to changing market conditions. Omron’s TM series of cobots are a good example of this versatility.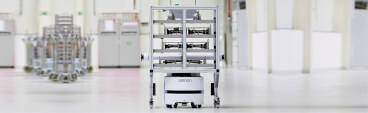
ŠKODA AUTO uses LD mobile robot at Vrchlabí plant
17 March, 2020 The autonomous robot contributes to the continuous improvement of work safety in Vrchlabí and helps to minimise work risks. It recognises people crossing its path as well as other vehicles and stationary obstacles.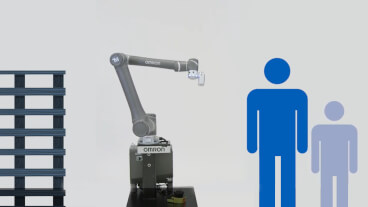
Safety in collaborative applications
10 February, 2020 Collaborative robots can be used in a wide range of industrial applications. Thanks to various integral safety features, they can work safely with or near people. In addition, they can easily adapt to changing needs. This results in increased productivity, especially in repetitive tasks, enabling manufacturers to reap the benefits of a high return on their investment. However, for a cobot application to be successful, it must incorporate safety considerations based on comprehensive risk assessments. So, what are the industry safety standards and solutions that will enable a company to gain the maximum value from cobots within a collaborative workspace?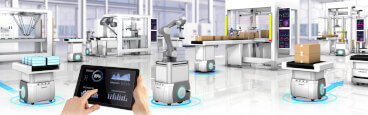
The factory of the future: people and machines working together in harmony
20 January, 2020 Automation and artificial intelligence (AI) are transforming the efficiency of industrial production, through stronger interactions between man and machine that can boost productivity. A new, promising model for ‘factory harmony’ is based on intelligent, integrated and interactive design for tomorrow's manufacturing processes.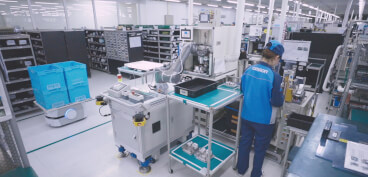
Humans and machine collaborate to meet today’s challenges
23 December, 2019 In Shanghai, labour costs are increasing by 7% every year. With growing shortages in manpower, it is becoming more and more difficult to hire factory operators. On the other hand, companies must consider return on investment and equipment effectiveness when adopting automation solutions in the factory.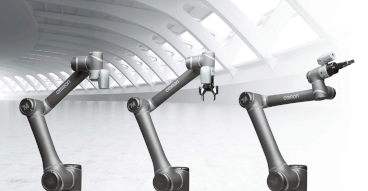
Three pillars of successful cobot deployment: safety, quality and flexibility from a single source
04 November, 2019 The use of collaborative robots is expected to increase rapidly in the next years to meet the needs of flexible production lines. To ensure that manufacturing layouts can be easily adapted to changing customer requirements, we recommend teaming up mobile robots and cobots. In addition, companies must consider integrated software apps and vision technology, as well as ensure support and risk assessment.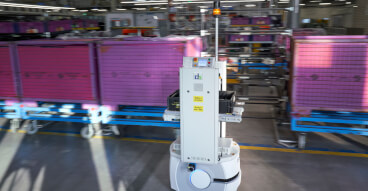
Agile and clever tailor-made mobile robotics
04 November, 2019 Major German automotive group optimizes efficiency and innovation leadership in material handling with Omron LD mobile robots and a conveyor attachment from cts GmbH.Automobile production and assembly line production have always been closely linked. It was not until Henry Ford began using conveyor belts in his factories in 1913 that the car was able to conquer the world as a mass-produced product. Today, a working day without assembly lines is inconceivable at the BMW factories. The group relies on innovative transport and logistics to increase efficiency and flexibility, to better link work processes, as well as to relieve employees from repetitive and time-consuming tasks. These concepts include Omron LD mobile robots for material transport that deliver a particularly high return on investment (ROI). These autonomous mobile robots are equipped with a conveyor tower - a height-adjustable load handling device, developed by system integrator cts GmbH. The interaction between employees and transport robots at BMW impressively demonstrates how factory harmony can be implemented in the factory of the future.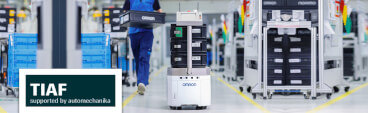
Top tips for choosing a mobile robot
16 October, 2019 In an age of short product lifecycles and an increasing demand for customised solutions, if you’re a manufacturer, you need to be very agile to remain competitive. For instance, you might need to make products down to a lot size of one as simply and cost-efficiently as in mass production; or to change or update your production line at short notice. One key solution is a greater co-operation between people and machinery, leading to improved efficiency and more flexibility in the design of the production line.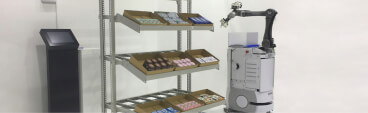
Autonomous bin picking with a collaborative mobile robot
16 October, 2019 Our TM collaborative robot provides a unique solution to easily automate applications such as picking and packing that, traditionally performed by humans, have been challenging to automate. As part of the TM series launch, we also released a mobile-compatible model, which seamlessly integrates into Omron’s LD series autonomous mobile robot. Combined with a 3D vision camera mounted directly onto the collaborative robot, this enables for example e-commerce companies to automate more complex tasks. This includes pick and place of various items onto a tray or container, as well as connecting production processes with the autonomous mobile robots for flexible manufacturing and materials handling.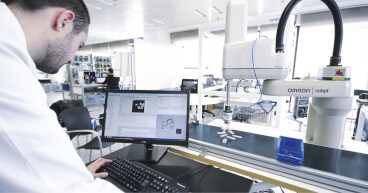
The power of collaboration between machines, people and teams
01 October, 2019 With today’s rapid advances in technology, the manufacturing sector needs to be increasingly agile, ready to adapt to changing demands. Production lines must be more flexible, so that they can cope with shorter production runs, more varied products and tight deadlines. So how can manufacturers address these challenges? The solution lies in more advanced, interconnected and intelligent systems that can be programmed to handle a range of tasks.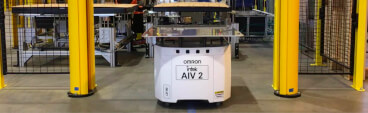