Beyond tech for tech’s sake: What happens when industrial automation meets operational excellence
Published on 30 November, 2024 in Operational Excellence
The past few years have seen rapid technological advancements, with the rise of AI standing out as a key trend. In a survey of manufacturers across the UK, US, and Canada, 70% said they had implemented some form of AI into their operations. This willingness to embrace new technologies is impressive, especially since manufacturing industries have so much to gain from automation.
However, for some companies, the motivation for adopting new technologies is driven more by the fear of being left behind, rather than a true understanding of how these tools can support broader business goals. To benefit from the promises of technology, manufacturers must move beyond adopting tech for its own sake. Simply adding new technologies to existing processes and systems will not automatically lead to improvements. Technologies like AI, machine learning, IoT, collaborative robotics, and advanced analytics will only create value if they are fully integrated into the company's culture.
At OMRON, we understand this deeply. For us, technology serves a greater purpose. It is not a destination in itself, but a tool to fuel continuous improvement—a principle that has been part of OMRON's DNA since its inception. Our founder, Kazuma Tateisi, believed in the relentless pursuit of improvement and innovation, in search of benefit for society. One of his favorite phrases, “Try it first,” demonstrated his belief that there is always a way forward if we embrace challenges with an open mind and a can-do attitude.
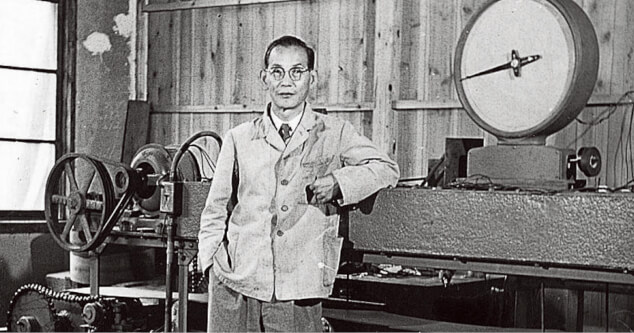
Technology-informed operational excellence
This spirit of continuous improvement is of course at the heart of operational excellence (OpEx). This is when the possibilities for increased production efficiency, flexible manufacturing and accelerated innovation become really exciting. This business management approach aims at activating the entire organisation and creates a culture where management and employees are invested in business outcomes and empowered to implement change.
Kazuma Tateisi also said, “If there is room to improve, then improve.” This was never just a slogan; it was a call to action that shaped OMRON’s approach to automation. We believe that the real value of technology lies in its potential to empower people, enabling them to think creatively, improve processes, and push boundaries. It is this alignment of technology and human ingenuity that creates the most meaningful innovations.
There are numerous examples of how the industrial automation innovations that have been born from this philosophy can be implemented to make a positive contribution to operational excellence:
Empowering people through automation
One of the ways we see this in action is through robotics and collaborative robots, which allow us to make use of the synergies between human talent and technological capabilities. This collaboration improves production efficiency and enables flexible manufacturing, where humans and machines work seamlessly together. Machine learning and AI are key to a harmonious human-machine future, in which robots learn instruction patterns from humans, move intelligently to assist with manual labour, and interact with humans and other robots.
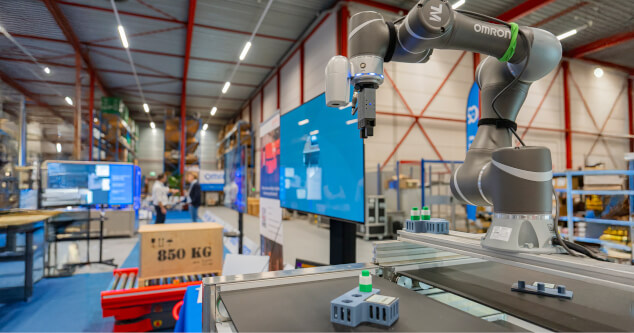
Continuous improvement with digital twins
Digital twin technology is another example of how industrial automation can drive continuous improvement. Creating a virtual twin of a machine or line allows design, process and system improvements to be tested without disrupting actual production. Projects can be de-risked and cost-optimised and the time it takes to develop, build and test the installation can be dramatically reduced. Digital twin technology also empowers line-level personnel to input into decisions about new products and new purchases, and to identify better ways of operating. In short, a digital twin supports continuous improvement by informing decision making and making it easier and more cost-effective to make changes.