German medical technology expert Senova cooperated with OMRON and Kraus Maschinenbau GmbH to pioneer the factory of the future.
Retail, manufacturing and public sector organizations across the globe are turning to technology to provide solutions to the coronavirus crisis. Innovative robotics, sensors and artificial intelligence (AI) technologies are all being used to accelerate processes and improve compliance with hygiene requirements. But to make inroads in the battle against the virus, companies need to form partnerships with organizations that have expertise in these areas.
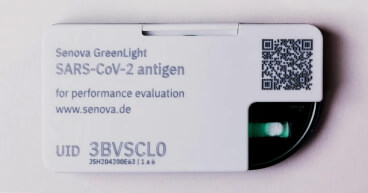
One example is the work conducted recently by German medical technology company, Senova, in conjunction with robotics experts from OMRON and mechanical engineering specialists from Kraus Maschinenbau GmbH. Senova is a leading developer and manufacturer of rapid test systems for marking biomarkers, viruses and microorganisms, including lateral flow assay (LFA) technology. Kraus specialises in solutions for dispensing, counting, separating, feeding and positioning paper and flat products.
Over the past six months, the three companies have developed production machines that include smart robotics. These have automated and streamlined the very time-consuming manual production of coronavirus antibody tests. This was vital, as rapidly increasing demand meant that Senova had to speed up the production of the test kits as well as developing more interlinked production and packaging.
Faster production of antibody tests
Senova’s most recent product is a rapid COVID-19 antibody test. This shows within ten minutes if someone has been infected with the virus. The test was developed by an international research team. A blood sample is used to show whether someone is infected or is already immune.
Senova brought the first coronavirus antibody rapid test to the market in record time. It helps people, including healthcare professionals, to know if they have immunity. Due to the worldwide demand for the new tests, Senova needed to ramp up production so that it could keep up with the thousands of orders. It needed a more flexible, reliable and faster way of manufacturing and packaging the test kits. Automation would streamline many of the processes (such as cutting the test strips and packaging). The changes had to be implemented quickly to meet the increasing demands and to reduce the spread of the virus.
Senova and Kraus developed a concept for feeding and packaging the cassettes used for the rapid antibody test. The precise cutting of the test strips and their insertion of into the test cassette are now performed by machines from Kraus. The processes are enhanced by robotics and technology from OMRON.
Robots that make a difference
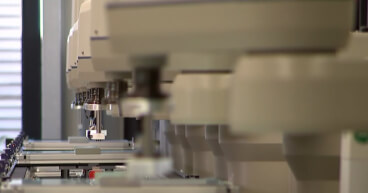
With the help of the new machines, 30 to 45 rapid coronavirus tests can now be cut and packaged per minute. Further machines are now planned to meet the ever-increasing demands. OMRON’s eCobra600 robots were chosen for the precise processing, assembly and material handling used in medical technology. The four-axis robot has a range of up to 800mm. The eCobra technology offers high repeatability and a payload of up to 5.5kg.
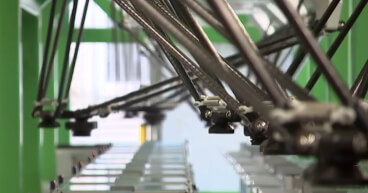
Other OMRON devices include Quattro 650 H robots, which can be controlled by Ethernet. The four-axis arm distributes the load evenly to the robot, enabling fast and high-precision transport and assembly. The robots are designed for high payloads and several parts can be picked up simultaneously, speeding the production of the coronavirus test. The control of the cutting and packaging machines also comes from OMRON, and is built into the Kraus production lines.
OMRON TM5-700 cobots designed to work with people and machines are also part of the solution. The cobot has an integrated image processing system, which enables quick product changes. As well as increasing productivity, it can be taught different tasks: for instance, relieving employees of repetitive work such as test cutting and packaging. The integrated vision camera and lighting technology enables objects to be detected precisely, enhancing the reliability, consistency and accuracy of processes such as pick-and-place.
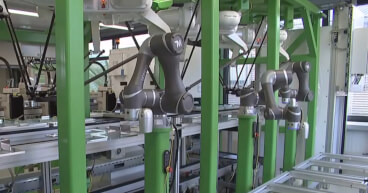
For cutting and packaging the test strips, the preliminary products are fed to the line, separated, positioned and placed in a servo linear unit. They can then be cut precisely. The robot inserts the blank into the plastic test cassette and assembles the front and back. The machine for packaging the rapid antibody tests then takes over the test cassettes. The pre-assembled packaging pouches are separated by a friction feeder and dispensed onto the packaging machine and the product labels are applied. Another robot inserts the test cassette into the pouch, which is thermally sealed and transferred to the delivery belt.
Success through co-operation
Christoph Waldenmeier, OMRON’s Sales Project Consultant, comments: “The latest generation of COVID-19 tests are now produced in a new production hall. The production lines are fully equipped with OMRON technology. We are pleased that we can use our technology to support the global efforts in the fight against the coronavirus to a small extent."
Joachim Kraus, Managing Director of Kraus Maschinenbau, adds: "The fast and uncomplicated implementation of this challenging project was only possible thanks to the excellent interaction and chemistry between the customer, machine builder, and system and control supplier."