Cobot solution with small footprint and active safety equipment enables handling up to 8 boxes per minute without the need for fencing or laser scanners.
Collaborative robots (cobots) are being used in a wide variety of applications. One recent example comes from a partnership between FlexLink and OMRON. FlexLink offers flexible, modular conveyors and industrial automation equipment, including palletizing solutions, to hundreds of customers across the world. You can find FlexLink solutions on the production lines of major brands in food manufacturing and personal care. Following a request from a major manufacturer, the two companies joined forces to create a collaborative palletiser, using OMRON cobots.

Stéphane Chevalard, FlexLink’s Engineering Supervisor, demonstrates the benefits of the solution: “Palletisation using cobots has a wide variety of benefits. First of all, it's very flexible. The system can be easily moved from one area of production to another. It can even be swapped between lines, because it’s self-supporting and easy to move. It also allows collaboration with operators, who can work in safe proximity to the cobot without fencing or laser scanners due to the active security we’ve added, which has enabled us to gain CE certification.”
Developing the system
OMRON and FlexLink were both involved in the initial design of the project, and the solution is continuously evolving as they receive feedback from users. The development of the system took place over several months, to ensure that end result would be flexible and easy to configure. The palletising system can process both US and Euro standard pallets, up to a height of two metres, thanks to the accessories that have been added.
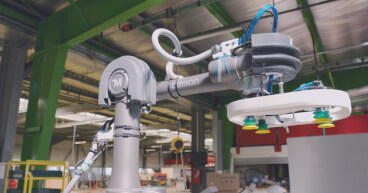
The cobot has a capacity of up to 8 boxes or parts per minute (ppm); or 14ppm with a dual-pick vacuum gripper. The new palletising systems can handle boxes of 10kg or 12kg, as two different types of cobots can be used - the OMRON TM12 or the TM14.
Gary Hinault, Flexlink’s Controls Engineer, comments: “This solution meets the need for automated palletisation, which relieves the operators from this repetitive task so that they can focus on tasks with more added value, and that are more interesting.”
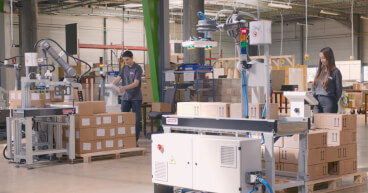
The cobots can be delivered in a fairly short time and the installation takes just one or two days. The automated palletising system helps operators to avoid the risk of musculoskeletal disorders or injuries caused by lifting heavy loads. The manufacturer who originally requested the cobot has calculated the return on investment for the new system as being about one and a half to two years.
For more information, visit www.flexlink.com