- 0:00 - Autonomous mobile robots simplify intralogistics at Diva International
Thanks to autonomous mobile robots (AMRs), the process at Diva International, a producer of personal care and cleaning items, is now safer and more efficient, keeping track of each step - from the order through to fulfillment in the warehouse.
Large companies are increasingly turning to robotics to streamline manual processes in factories and warehouses. One example is Diva International, based in Umbria, Italy. Diva wanted to transform its system for transporting wet wipes from its production facility to a palletising island in the same warehouse. Through its facilities management provider, FM Vision, it developed a new, automated system using five OMRON autonomous mobile robots (AMRs) and OMRON’s Sysmac NJ machine controller. This has led to a safer, more efficient and more flexible process.
Diva needed a system that would optimise the use of current space. It also wanted to keep track of each step of the process: from the order through to fulfillment in the warehouse. This was made possible by the five OMRON AMRs, which load and unload packaged batches of wet wipes from the end of the line to the palletising stations.
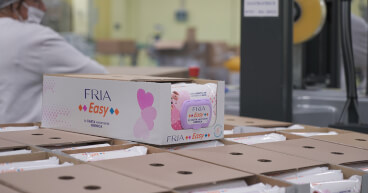
A challenging situation
In developing the new system, FM Vision and OMRON faced various challenges, particularly in relation to safety, speed and cleanliness. The key challenge was to design a system for loading 12 cardboard boxes in the shortest possible time, whilst managing 60 different formats and a wide range of weights.
Augusto Falchetti, Owner of FM Vision, observes: "A sorting and conveyor system for packages with such different formats would have proved too difficult, due to problems of space, cost and safety. A flow of 120 pallets, each with 70 packs, means that over 8,000 packs needed to be moved each day."
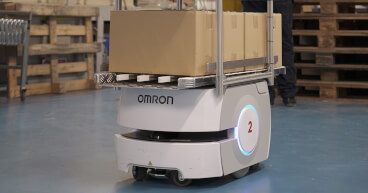
The production area also had to be kept separate from the palletising area, as it contains potential contaminants and due to the need to comply with fire regulations. OMRON’s five robots can move independently and decide which route to take, using a navigation system based on a map of the premises and a dynamic reading of the environment. The robots each have a laser scanner that enables them to ‘see’ the adjacent environment. Their movements are managed by a series of sensors and controls that enable them to avoid people and other obstacles.
Luca Polzoni, Diva’s Data Analyst, says: “All this translates into a dramatic reduction in waiting time. When an obstacle is detected on the path, the robot can always find an alternative route by performing a recalculation in real time.”
Another challenge involved the engagement and disengagement between the AMRs and the conveyor belts when loading and unloading. The design constraints meant that the robots weren’t allowed to move beyond 800mm from the conveyor belt.
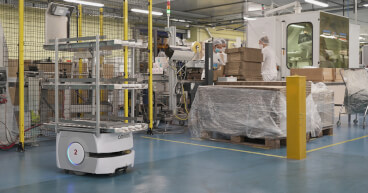
The frame of the fixed station has therefore been designed to have an adjustable height, with three levels, each able to manage a batch of four boxes. The positioning of the robots has to be calibrated to almost a millimetre, as there are very narrow tolerances of position and speed. The robot’s movement must be precise: even one degree of error could compromise the process.
A streamlined process
OMRON’s Sysmac machine controller guides the whole process, from the arrival of the order through to the sorting of packages on the palletising islands and their dispatch to the warehouse.
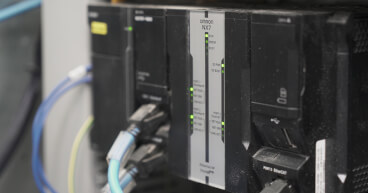
Paolo Capezzuoli, Field Application Engineer Motion Specialist at OMRON Industrial Automation Europe, comments: “The most complex aspect involves the wireless communication with the AMRs for generating jobs. This activity passes through a fleet manager developed by OMRON that assigns tasks to the mobile robots based on certain conditions (such as battery level and proximity to the pick-up point). It also defines the most intelligent routes for avoiding collisions and reductions in speed.”
The new system has streamlined Diva’s logistics operations. Luca Polzoni says: “The mobile robots self-adapt to the available slots and have the necessary certifications, including safety, to operate in the same environment as the operators. In about one and a half minutes, they complete their journey, which averages 10 metres, plus loading and unloading, carrying a dozen packages to the palletising island.”
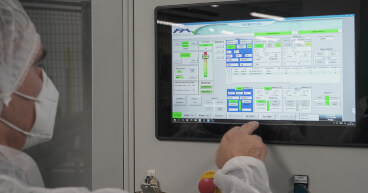
As well as boosting efficiency and freeing up employees, the new automated system has helped to eliminate human errors relating to data management. Paolo Cocchioni, Diva International’s Commercial Director, concludes: "For a world leader in the sale of wet wipes, it’s essential to be able to rely on a level of automation that can support the production of about 60 million packs a year. This modernisation allows us to carry out the work even in the presence of staff, meeting deadlines whilst also complying with hygiene and safety rules."