Lights out? Still unlikely with Industry 4.0
Published on 21 April, 2022 in Industry 4.0
Digitalization isn’t binary
Certain situations clearly favour a (human) hands-off approach, such as Foxconn’s complex production of electronic components, and in areas where contamination risks are high, as well as in many types of high-volume, low-mix plants. But what about those manufacturers not running this way, instead moving a low-volume, high-mix to maximize customer choice? Is their route to automatization blocked by their need to diversify? Thankfully, no.
Finding the right roles
Today there is a growing shift to production lines where manufacturing staff are put to work in roles where their skills are most valuable: in supervisory areas, rather than the traditional operational duties. This, and working with collaborative robots (cobots), where human speed and dexterity are aligned with the tireless efficiency of the automated companion worker.Proof of concept
From system analysis to full on proof of concept, covering separate line applications to entire facilities, trusted integrators are the first point of contact for manufacturers seeking improvement. OMRON also offers its services in this process, and its proof-of-concept laboratory and high-tech facilities where prototype systems can be built to demonstrate exactly how manufacturers can benefit from automation. So, what can manufacturers expect?
A digital look ahead
Machine vision is a growing field of automation, with advances in 3D vision systems increasing the flexibility of complex pick & place operations. Until relatively recently, cameras were only able to process products in fixed positions on the line. Today high-resolution cameras coupled with machine-learning algorithms can now readily identify objects randomly positioned in transport bins. This greatly increases the viability of camera systems for varying products, running at increased speeds, on automated lines.Advances in robot technology
Whether it’s a mobile robot to replace a forklift, or a cobot to work alongside a human operator, the efficiency and reliability of repeatability here is being seen in an increasing range of industries. Cobots for instance are simple to program, particularly when compared to more traditional industrial robots, and are easy to re-deploy for different tasks, which is a particular advantage in high product-mix scenarios. Where high-speed repeatability is the goal, industrial robots – such as delta robots – are ideal. Here, recent progress in tooling has advanced the automated packing of fruit, with new gripper designs allowing automated soft fruit packing with industrial robots for the first time.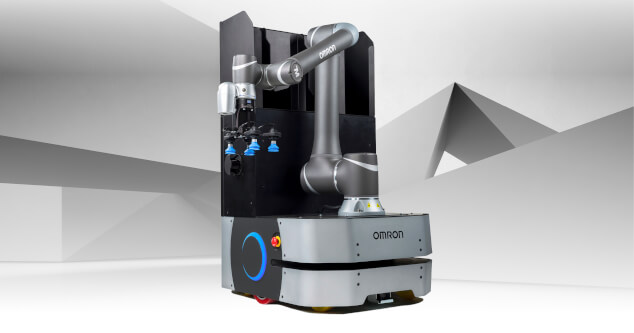