Joining the dots: Automating feeding activities for a competitive advantage
Published on 18 June, 2024 in Flexible Manufacturing
Factory automation usually starts with the dots. By this we mean the big ticket plant that performs complex and visibly value-adding tasks - whether that is flow wrapping, injection moulding, blister packing, bottling, palletising or other core manufacturing processes. The lines that join those dots together - handling, loading and feeding systems - tend to be more of an afterthought, to the point where these activities are often carried out manually.
It might seem easier and cheaper to have an operator loading raw materials onto the production line, or feeding components into machines, rather than spending on automation. But this is a shortsighted view that misses the many business benefits that automated line-side feeding and handling can deliver in terms of efficiency, product quality, scalability and health & safety. It is also a view that is increasingly outdated given the pressure that the current labour crisis is exerting on the manufacturing sector.
A shrinking labour pool
In this climate of labour shortages and escalating costs, automation is emerging as a strategic imperative for businesses seeking to achieve sustainable growth. And that means paying attention to not only the dots, but also the lines that connect the dots. Indeed, investments in technologies such as robotic automation, machine vision, material handling systems and smart feeding solutions hold the key to enhancing manufacturing efficiency and mitigating the risk of labour shortages.
Autonomous and collaborative approaches
Collaborative robots (cobots) and Autonomous Mobile Robots (AMRs) are two automation tools that have transformational potential in this respect, and going forwards we expect them to become more prevalent in automated feeding and handling strategies. These sophisticated machines fuse human expertise with machine precision, ushering in an era in which automation is not just a tool but an indispensable component of manufacturing excellence.
Having embraced the fourth industrial revolution, marked by the convergence of digital technologies and physical systems, the manufacturing industry is now moving towards Industry 5.0. In this paradigm, robots and machines work alongside people, while sustainability and resilience goals add a further dimension. Cobots, with their collaborative and adaptability capabilities, will play an important role in transitioning to this new way of working.
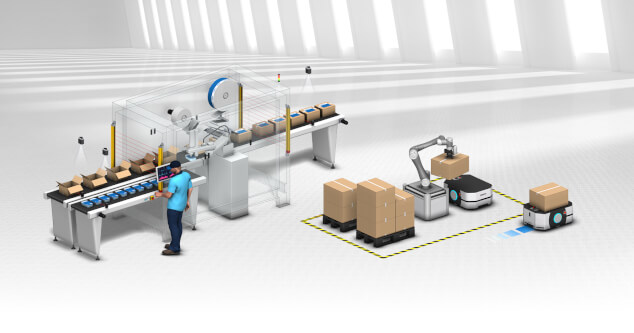
Supporting tech drives performance improvements
Similarly, the agility and flexibility of AMRs to navigate dynamic production landscapes with precision, delivering components precisely when and where they are needed, makes them a strong candidate for integration into material handling and logistics systems. And as with cobots, advancements in supporting technologies are driving performance improvements and increasing the potential of AMRs to add value. For example, as LiDAR and Simultaneous Localisation and Mapping (SLAM) continue to evolve, autonomous navigation capabilities will be further refined, optimising travel routes and minimising cycle times. This heightened efficiency and responsiveness will empower manufacturers to adapt swiftly to changing demand patterns and production requirements.
There is also a huge opportunity to harness the synergies that exist between cobots and AMRs for operational optimisation and manufacturing competitiveness. By taking advantage of the complementary strengths of both types of robotic systems, manufacturers can achieve unparalleled levels of agility efficiency, productivity and quality in line-side replenishment processes.
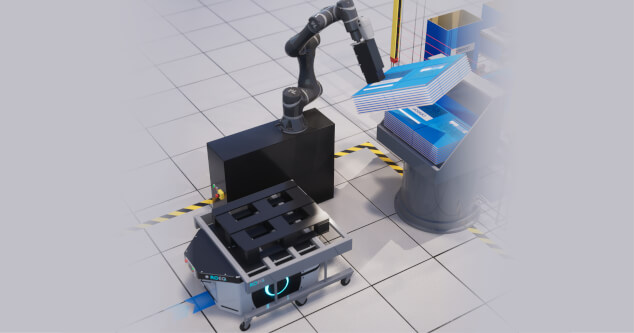
Fischer Gears: a case in point
The benefits of embracing cobot technology are in evidence at Fischer Gears, where the implementation of OMRON TM cobots has had a significant impact on production efficiency, labour utilisation and overall profitability. By automating the feeding process for metal parts into CNC machines, the company has optimised its production line, allowing seamless operation even beyond regular working hours. This enhanced efficiency has given the company a competitive edge in fulfilling orders of varying sizes.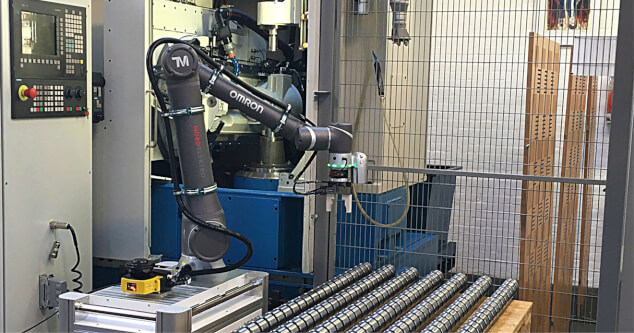
Lessons learned
Firstly, it is essential to thoroughly assess the specific needs and challenges of the production process before implementing automated solutions, This involves identifying bottlenecks, analysing workflow inefficiencies and evaluating potential ROI to ensure alignment with business objectives. Understanding the challenges of manual handling is the key to devising effective strategies to overcome them.
Secondly, investing in advanced technologies that may, on the face of it, appear to push up the project cost, is worth doing. Intelligent vision systems and safety features, for example, enhance the effectiveness and reliability of automated feeding systems, ensuring smooth operation and mitigating potential risks.
Finally, continuous monitoring and optimisation of automated processes is essential for long-term success. Regular performance evaluations and data analysis enable companies to identify areas for improvement and drive ongoing innovation in automation.
