The safety network in the semiconductor manufacturing equipment is important for process optimization, yield improvement, and quality control. Our safety control system, developed over many years, enhances yield and maintains the quality of the process tool.
Application: Safety control by open network protocol
As equipment evolves, the need for networked safety control has increased from traditional hard-wired safety control. However, it is very difficult to control the equipment itself by using separate networks for safety control and standard control within the equipment.
Our Solution: Programmable Safety System
OMRON offers a programmable safety system with an open network. By using Safety over EtherCAT (FSoE), we enable the integration of both safety and standard control systems. This makes it possible to manage the control and safety systems together, instead of separately.
The shift to equipment control using a network can contribute to future equipment scalability, such as an increase in the number of I/O points and unifying the network with EtherCAT can also improve the data processing capacity of the entire equipment.
Enabling Technologies
Safety Open Network Protocol
By using the Safety over EtherCAT - FSoE - protocol, we can integrate safety control into machine control through open network technology. Both the safety controller and the safety I/O can be freely distributed in an I/O configuration throughout the network, mixing them in any combination with standard NX I/O.
Related Products
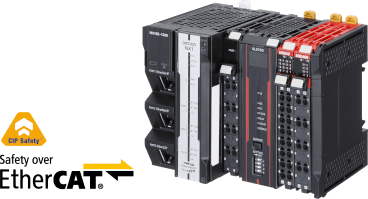
From single machine to production line all, safety interconnect
Quick, easy, and flexible to integrate safety into production lines combining two different integrated networks, EtherNet/IP (Common Industrial Protocol Safety (CIP-S)) and EtherCAT (Safety over EtherCAT (FSoE))
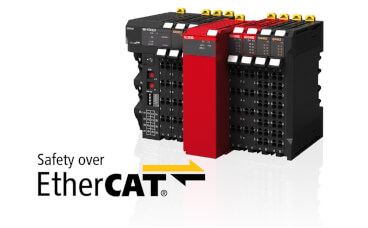
Integrated safety into machine automation
The Sysmac automation platform integrates the safety solution within our one connection and one software concept. One connection is realised through the use of Safety over EtherCAT - FSoE - protocol. The one software is achieved by using the Sysmac Studio for configuration, programming and maintenance. The NX safety system consists of safety controller and safety I/O units. Both the safety controller and safety I/O can be freely distributed in an I/O rack throughout the network, mixing them in any combination with standard NX I/O.
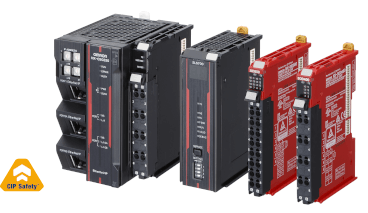
From a production line to a single machine safety solution
Quick, easy, and flexible to integrate safety into production lines
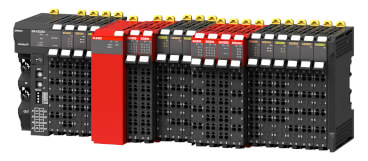
NX Stand-alone Safety Controller
NX-Safety Stand-alone is a powerful, modular and easily commissioned safety controller which, due to its scalability, can be efficiently adapted to the requirements of a wide variety of safety applications. Thanks to this modular and expandable hardware, the compact safety controller grows with its task slice-by-slice – right up to the highest safety level. You can grow up to 256 I/O points in one single Safety CPU. The design of safe system solutions is thus considerably simplified.
Do you want to know more?
Contact Our Experts
Contact Our Experts Safety Network
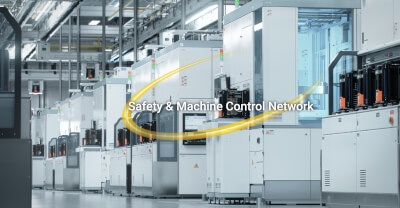
Thank you for submitting your request. We will come back to you as soon as possible.
We are experiencing technical difficulties. Your form submission has not been successful. Please accept our apologies and try again later. Details: [details]
Download