Some companies lead the way in terms of being visionary and making use of the latest technology. One such organisation is Picomel Nutrition, based in Zeewolde, The Netherlands. Picomel develops and produces high quality, private label bottle food for babies, toddlers and pre-school children. It provides the packaging and also produces a unique private label formula for babies who need a special diet. Some 40% of Dutch infants are given nutrition developed by Picomel.
Jan Kees Verhage, founder of Picomel, envisioned and designed the company’s ‘vertical’ factory. It’s the only factory in the Netherlands to gain a 'BREEAM-NL Outstanding' sustainability certification. His creative vision meant that he also wanted to develop the machine of the future – today. To achieve this, he enlisted the help of machine builder Van Mourik, along with automation technology from OMRON Industrial Automation.
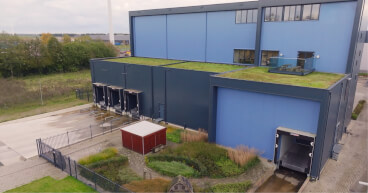
Jan Kees comments: “We were looking for a company that could help to provide a total solution for automation. We also needed strong technical support, from proof of concept until realisation of the project. Van Mourik recommended OMRON to us, and OMRON’s solutions provided the answers needed for the challenges we faced.”
Setting the standards for the new machine
Picomel, Van Mourik and OMRON worked closely together to develop a new type of machine. To adapt to the challenges and issues in the market, Picomel devised a set of requirements for the machine that he wanted to build. It needed to be high capacity but with a small footprint and fast changeovers. It had to be able to handle multi-format products and various can sizes. It also needed to be intuitive, so that operators wouldn’t have to go through an intensive period of complex training. Finally, it needed to be scalable, with no waste and less noise than comparable machines.
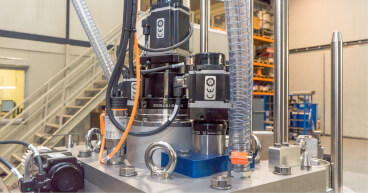
Creating the new machine
Jan-Kees adds: “Every extra metre square of footprint has it costs. We wanted to reduce space and costs by building a vertical factory. We also needed more compact machines. We therefore got together with machine builder Van Mourik and OMRON’s technological experts. The result was a Servomatic machine. This is a fully integrated can powder filling and seaming machine that boasts the world’s smallest footprint (6m²) whilst providing a high output. A traditional factory would need four to five times more space to achieve the same capacity.”
Martin Dannenberg, Managing Director at Van Mourik Yeast & Packaging comments: “After in-depth analysis, we discovered that we needed servo technology to properly control this process. Thanks to this control, and the fact that the machine is relative easy to convert to other formats, we can achieve vertical start-up. This means going from zero to full operational capacity in a very short period of time.”