Securing a battery-powered future through automated recycling
Published on 17 December, 2024 in Sustainable Manufacturing
Batteries have a crucial role to play in facilitating the scaling up of renewables in the power mix and the electrification of transport, as we transition away from fossil fuel dependence and towards cleaner energy technologies to meet the targets agreed at COP 28.
This has sent the battery market on an upwards trajectory, with two sectors - power and transport - driving demand. According to the International Energy Agency (IEA), the energy sector accounts for over 90% of overall battery demand. It reported that in 2023 alone, battery deployment in this sector increased by more than 130% year-on-year, adding a total of 42 gigawatts (GW) to electricity systems around the world. Energy storage is emerging as a major application for batteries as a means of capturing renewable energy and is only going to become more important in the future. In the transport sector, meanwhile, batteries have facilitated the rise of electric cars, bikes, trucks, buses and other battery-powered vehicles.
Raw material insecurities
However, the future growth of battery manufacturing and the industries it serves will be highly dependent on securing a reliable supply of materials such as lithium, cobalt, copper, nickel, manganese and graphite.
At present, China dominates not only the production of batteries, but also the supply of raw materials, as it owns most of the mines in Africa, Australia and South America. Although Europe has its own reserves of battery raw materials, these are not yet being exploited, and the process of opening a mine takes years not months.
The other route for obtaining raw materials is to recover them from batteries that have already been built. In theory, this offers a promising strategy for Europe to reduce dependency on precarious global supply chains and establish sustainable closed loop production. However, the reality is that the recycling of batteries is fraught with complications.
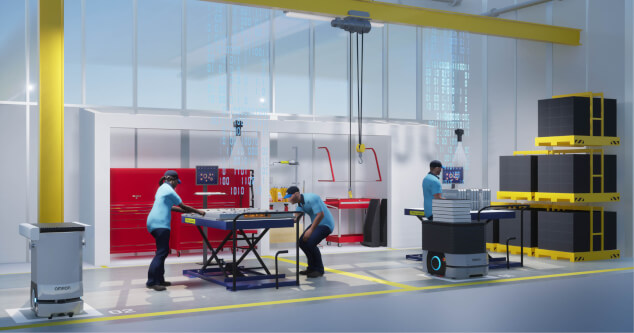
Battery recycling challenges
The main problem is the lack of standardisation in battery chemistry and construction. Today, nobody really knows what is inside the batteries that are in circulation. Recyclers have built up databases that they can consult to identify the battery model and to determine the materials used in a particular battery, but even if they find a match there are no guarantees that the anatomy of the battery in front of them will tally with the database. Over its lifetime, a battery will undergo irreversible chemical and structural changes that may result in material degradation. Equally, changes in raw material suppliers during the lifecycle of a particular subtype could lead to changes in composition.
Quality is another issue for recyclers looking to extract and recover raw materials from batteries. Lithium, for example, has to be 100% pure to be reused - if it is contaminated even very slightly during the recycling process, this will render it unfit for reuse.
Another issue is that not all batteries are returned in good condition, and damage is not aways visible, making it difficult for recyclers to assess their condition. It may be that a car battery has been in an accident, or that the nodes in an electronics battery have washed off, both affecting battery recyclability.
Suitable for a second life?
Battery recycling is not just about recovering raw materials for the production of new batteries, it is also about repairing and repurposing batteries for second life applications. Once the capacity of a battery falls below 80% - the level that is considered acceptable for electric vehicles, there’s no reason why it can’t be given a second life as part of an energy storage solution.
This, however, comes with its own set of challenges, and recyclers have to go through a long decision-making process to identify whether a battery is suitable for second life applications before cracking it open. They also need to ensure they have enough of the same batteries for large capacity energy storage projects, where mixing battery types is not an option.
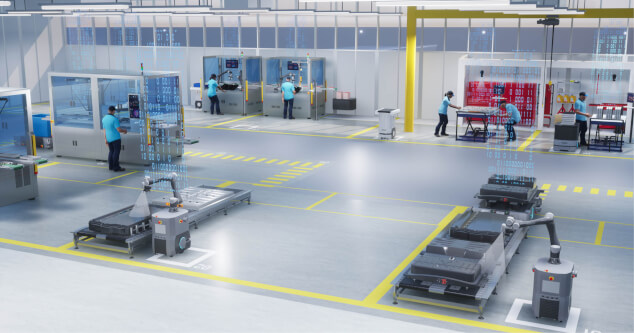
Battery sorting and dismantling: a manual operation
Due to the many challenges, the dismantling of batteries for recycling still remains an entirely manual process. Essentially it is a reverse manufacturing process, in which the electronics and the chemicals have to be removed separately. This is not only a slow, arduous task when performed manually, it is also a dangerous one. The battery has to be discharged before it is dismantled, as if a worker comes into contact with the active parts of a charged battery, they could suffer a severe electric shock. The presence of poisonous materials such as solvents and electrolytes is also a serious health & safety risk when handling batteries.
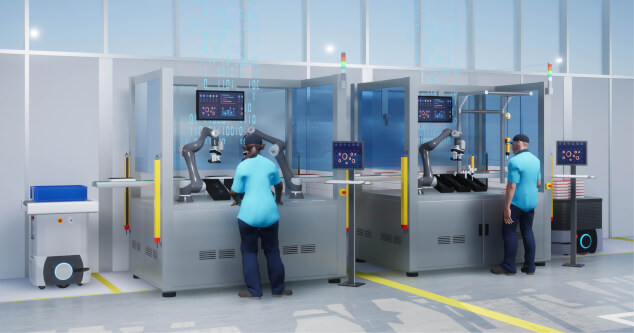
The EU Batteries Regulation
The new EU Batteries Regulation represents a huge step towards establishing a circular economy for batteries and their component parts. As well as introducing targets for recycling efficiency, material recovery and recycled content, the legislation includes several requirements that will go some way to addressing the issues that recyclers currently face.
One stipulation is that batteries used in vehicles and electronics need to be removable. This will not only extend the life of these products, but will also make it easier to remove batteries for recycling purposes.
Another requirement is that from 2027, all electronic vehicle and industrial batteries over 2 kWh sold into the EU market will require a unique battery passport retrievable via a QR code. This will be a game-changer for battery recycling as it will eliminate many of the uncertainties around battery composition.
However, there will be a considerable time lag before digital passports are of practical use for recyclers. Batteries have a minimum lifespan of eight years, with their actual lifespan usually closer to 15 years. This means that the first batteries with digital passports will be available for recycling from 2035 at the earliest, and that batteries without passports will still be in use in 2040. In the interim, there is an urgent need for the advancement of technology-based condition testing and measurement techniques.
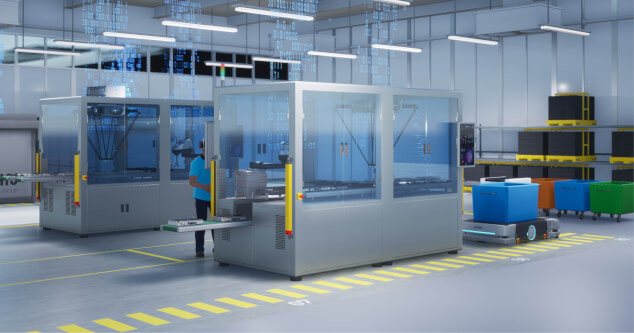
Automation has revolutionary potential
Intelligent automation holds the key to the safe and efficient sorting and dismantling of batteries, to enable them to be easily recycled. Vision and sensing technology can be combined with data analytics and AI to identify the battery type; robots can perform dangerous tasks such as opening, discharging and dismantling the battery, without putting human workers at risk, and digitalised processes can support the separation of the so called ‘active mass’.
OMRON is a partner in the German DiLiRec research network, which, over the next three years, will focus on developing sustainable recycling processes for the cathode material lithium iron phosphate (LFP). Efficient battery cell sorting, dismantling and electrode stripping, as well as the systematic recording of data in the battery recycling sub-processes, have been identified as pre-requisites of efficient LFP recycling. OMRON brings capabilities in robotics, data-analytics, and AI-powered vision and sensing to the eco-system, which brings together battery manufacturers, researchers and recyclers.
Europe’s lack of autonomy in battery production is threatening the future growth of its electromobility and energy industries. The advancement of the region’s battery recycling infrastructure is key to securing the supply of raw materials these industries need, as well as creating the circularity that is needed to realise the sustainability potential of battery-powered technologies. Automating the sorting and dismantling of batteries is a tiny but crucial piece in this jigsaw, and OMRON is proud to be part of a movement that is driving the shift to a new paradigm.
Contact us for more information