Monitor machine stability with data science
Published on 16 July, 2021 in Industry 4.0
Sanity check for your machine
How does this scan work? Signals from sensors and (where possible) actuators will be logged on a high frequency, analysed and linked to the machine process and control program. By doing this together with the machine operators and/or engineers, you get detailed insight and can spot deviations and inconsistencies, such as sensor misalignment, misconfiguration and worn-out parts. Think about reducing the micro stoppages or finding out the root cause of an intermittent and indistinct problem.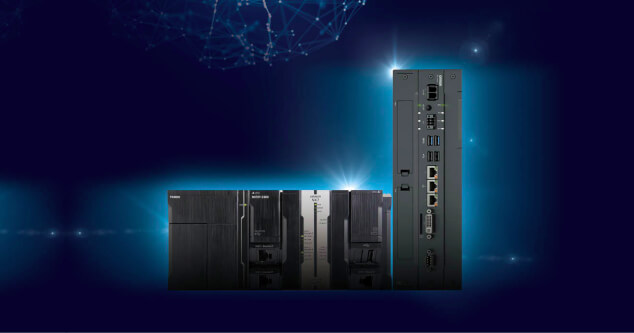
Machine monitoring
With constant monitoring it is possible to detect process and quality anomalies, to discover trend drifts and to give advises for predictive maintenance. Your machine changeover time and more input data for model training becomes available. A regular update of the models is necessary to keep and enhance the accuracy of predicting.Putting OMRON’s Sysmac AI Controller to work
Did you know that OMRON has a machine controller with a Sysmac library for artificial intelligence? We can support with a Proof-of-Concept and assist during the implementation of the AI-Controller on your line. OMRON can also offer you AI-as-a-service where we will take care of the complete implementation, updates, upgrades, and maintenance. Even AI systems need regular attention to improve and adapt to the detected changes in machine behaviour and/or production process.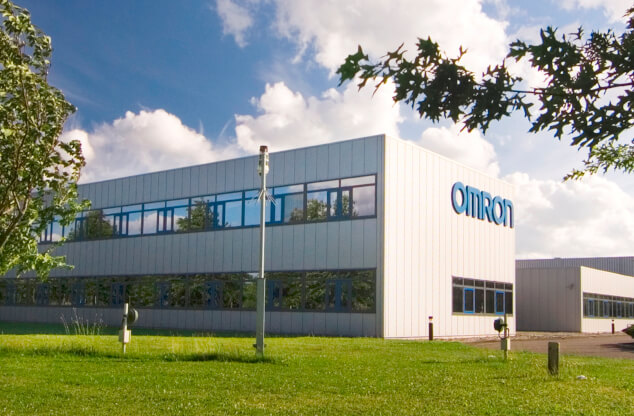
Case study: OMRON Manufacturing of The Netherlands
Recently, a Data Science project was performed at the OMRON Manufacturing of The Netherlands (OMN) factory on the NX assembly line, focusing on the pin stitcher machine that stitches pins into plastic casesThe pin stitcher machine contains several motors and sensors that generate more than 50 signals in parallel. The goal of this project was to monitor all the signals at the same time and discover abnormal situations. The AI Controller captured signals every 2 milliseconds as event data and stored them for data analytics and anomaly detection.
One of the common issues in the pin stitcher machine is caused by bending and reel feeding motors when the machine does not move the reel in the right way. This problem needs a maintenance activity which stops the whole production line for almost one hour. With anomaly detection the faults can be detected early, and an alarm is sent to the engineers and maintenance. In the case of the pin stitcher machine, the alarm is set off a few hours before a major problem can occur. This early alarm prevents the standstill of machine because it ensures timely maintenance action and suggest simple correction without significant machine stoppage.
In addition, subtle changes in the machine cannot be detected by humans. If the machine slows down for each production cycle, just by a few milliseconds every week, this will not be captured by operators or engineers. Overtime, the machine could become 10% slower and produce 15% less in one day. The root cause of this issue was found through monitoring the behavior of all signals using anomaly detection models. Adjustments can be made to keep the machine performance at a high level.
Would you like to exploit the full value of your industrial data or do you have a problem for which you believe the solution is hidden in your data? Download the white paper below for more details.