Digitising with open standards: the recipe for a good night’s sleep
Published on 02 September, 2024 in Operational Excellence
These are some of the concerns that keep factory managers awake at night; concerns that can be addressed through digitisation. In a digitised production environment, factory managers don’t have to worry about the unknowns, the risks and the might-happens. Digitisation eliminates uncertainty and enables performance-driven optimisation. It provides insights that can help factory managers improve quality, reduce cost, shorten lead times and reduce environmental impact. The manager of a digitised factory shouldn’t wake up worrying in the middle of the night, but if they do, a brief glance at their mobile phone should reassure them that everything is running as it should be.
However, moving from a state of anxiety-induced insomnia to one of blissful somnolence is not easy. Put bluntly, digitisation can be quite tedious. Project leaders rarely have the luxury of working with a blank canvas; most of the time they are working with a patchwork quilt of old technologies sewn together; they are trying to digitise production lines incorporating machines that have never logged data and were built before data communication protocols even existed. This all adds up to a sizeable OT and IT integration challenge.
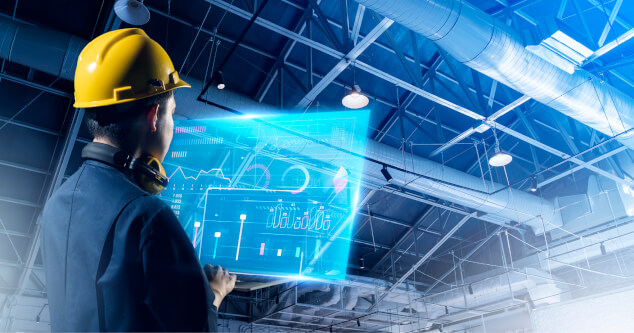
Aim for 80%
You can use non-open standards, but ultimately this will limit your ability to fully capitalise on the performance optimisation opportunities that digitisation presents and to communicate beyond the factory walls, which is why we advocate an open standard digitisation approach.
For collecting real-time machine and process data a common modelling language such as PackML will achieve standardisation. Successful digitisation also requires a standardised communication protocol so that machines can talk to one another and other Industry 4.0 components. OPC UA, a protocol that originates from the IT domain, is increasingly crossing over to the industrial automation sphere, and OMRON is part of an automation industry-led steering committee that is extending OPC UA to industrial field level devices called UPC UA FX.
The analogy I often use is with the English language, the universal language of business. If you speak English, you can do business with most people. The same principle applies to OPC UA FX in an industrial context.
This open standard supports complete interoperability within a factory. Not only does it allow machines to talk to each other in data terms, it also enables machines to talk to IT systems such as ERP and MES systems, as well as data analytics systems that you may be running on a local or virtual cloud.
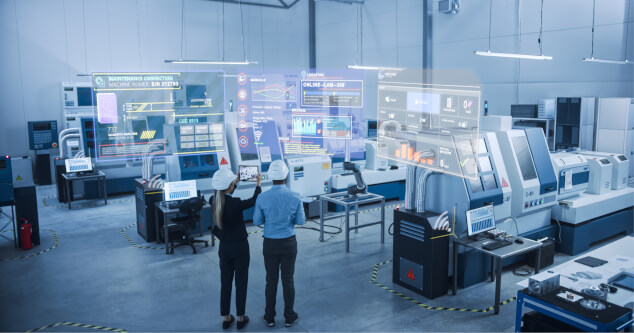
Opening up opportunities
Open standard digitisation is also key to deriving value from Digital Product Passports (DPPs). As well as being a legal requirement from 2027 for some industries, DPPs, which provide a digital record of a product’s composition, origin, and lifecycle, are a useful Industry 4.0 tool. In the production of batteries for electric vehicles, for example, DPPs could be used to improve quality and reduce waste. Combining components of the same quality has been found to result in a better battery. The reason this doesn’t always happen is because of variation that occurs within set tolerances. Using DPP data communicated via OPC UA, warehouses could pick individual components with similar characteristics and thereby reduce the risk of batteries failing factory tests and having to be scrapped.
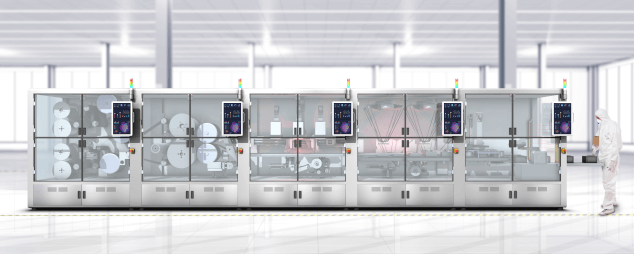
Digitisation is gaining momentum with growing awareness of the real world benefits that data-driven insights can bring. However, standardisation - in terms of the type of data being collected and the way in which that data is communicated - is a major challenge for factories looking to digitise industrial automation. By adopting an open standards approach, manufacturers can succeed at digitisation, and factory managers can sleep easy.