What’s in store for automation in 2024? Six predictions from OMRON Europe
Published on 13 December, 2023 in Operational Excellence
The succession of shocks over the last few years has heralded a new era of heightened geopolitical and economic risk. This is prompting manufacturers to build resilience and flexibility into business models and rethink global supply chains and relationships. At the same time, pressure is mounting to incorporate ESG principles into operational decision making. AI, data science, digital twins and sensing, monitoring and vision technology will all be essential to developing automation and control solutions that can help the manufacturing industry adapt to this new reality. In this context, I would like to share the top six trends that will impact and shape industrial automation in 2024 and beyond.
Trend #1 supporting local-for-local production
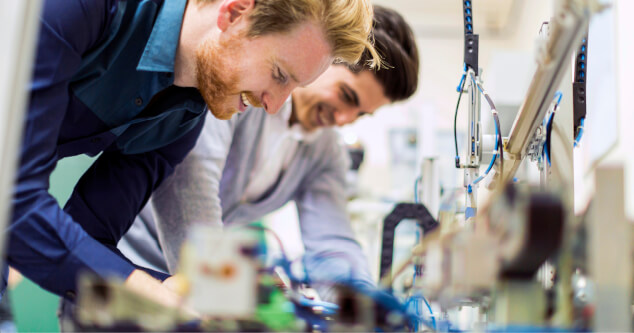
Trend #2 CX to the fore
Trend #3 connecting OT and IT to cost-optimise flexible manufacturing
The shift towards flexible manufacturing, which has been underway for some years, is gaining momentum and evolving as a concept for enabling manufacturers to pivot quickly if the need arises. HMLV manufacturing has reached new levels of personalisation - particularly in the pharmaceutical industry - and flexible workflows that can switch seamlessly between different products are characteristic of localised production. However, the main challenge with flexible manufacturing is making it financially viable. OMRON believes that connecting the OT world with the IT world is the key to optimising the cost of engineering and predicts that in 2024 and beyond, digital twinning will be widely adopted for this purpose. With digital twin technology, companies can re-engineer production and test changes in a virtual environment. Not only does this reduce development time, it also de-risks and cost-optimises projects.
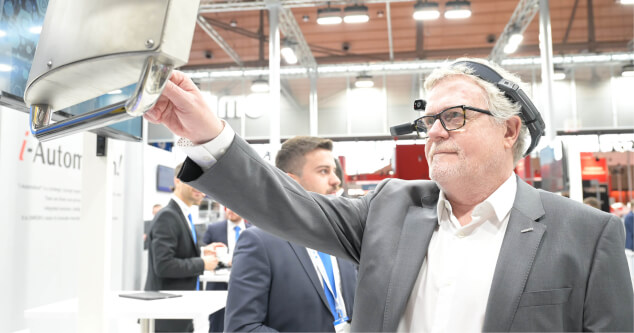
Trend #4 data analytics to inform sustainability-led decisions
As well as utilising virtual reality to optimise costs, manufacturers will increasingly rely on real world machine monitoring to make flexible, localised manufacturing operations more streamlined - and more sustainable. Manufacturers in all sectors are looking to reduce raw material and energy consumption and are looking to their automation providers for answers. In a factory setting, data acquisition and analysis in conjunction with high performance control systems can drive improvements in this area. To this end, OMRON has developed i-BELT, a service that uses the principles of the Internet of Things (IoT) and data analysis to improve the efficiency of automated systems.
Trend #5 sharpened safety focus drives automated inspection
Another challenge that accompanies flexible manufacturing is maintaining safety and quality standards. That is because, the more variables there are in the production mix, the greater the potential for errors and problems. In a world where brands are increasingly subject to public scrutiny and reputations can be destroyed in an instant, companies are taking safety more seriously than ever. This is driving the development of automated AI-powered inspection systems that ensure the safety, integrity and quality of each individual product - even in batch size one operations.
Trend #6 AI at the edge and beyond
In everyday life, the omnipotence of AI might be perceived as a threat, but in the domain of industrial automation, it represents a huge - and still largely untapped - opportunity to continuously improve system performance.
OMRON is applying AI ‘at the edge’, in robotics, controllers and vision systems. We are using it to identify very small defects in mirrored surfaces and to detect jams inside packaging machines. Our remit for AI is the production environment and we will continue to explore and advance its use in this.
In the next few years, the transition to a new paradigm of fully flexible manufacturing will dominate and guide the direction of automation developments. This will allow companies to deal with future supply chain challenges while meeting customer demands. In parallel we will see a move to more autonomous manufacturing, which prioritises quality, safety and sustainability.